Why do top-tier manufacturers secretly rely on an industrial laser cleaner for critical operations?
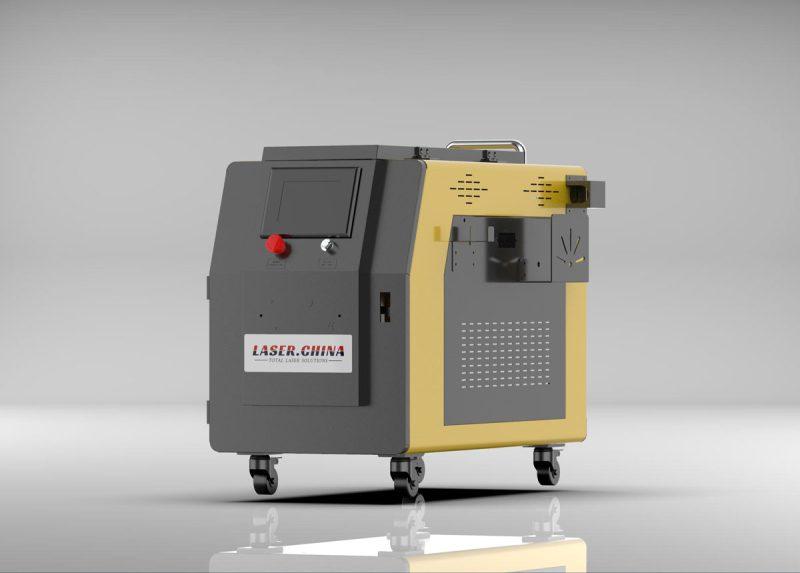
In modern industrial landscapes, precision, sustainability, and efficiency define competitiveness. Amid this shift, one tool has quietly gained dominance in critical cleaning operations—the industrial laser cleaner. Though not always highlighted in public discussions, major manufacturers in aerospace, automotive, defense, and electronics increasingly depend on this technology to meet exacting standards.
But why this silent adoption? And why does the industrial laser cleaner find its place in the most critical production lines? To understand this, we need to explore its practical applications, the industries that swear by it, and how it integrates seamlessly into highly regulated and performance-driven environments.
Why Surface Preparation Is Non-Negotiable
Before bonding, welding, painting, or coating, surfaces must be completely free from oxides, grease, rust, or residues. Traditional cleaning methods like sandblasting, chemical stripping, or grinding either damage the base material or pose environmental and health risks. Moreover, they require significant downtime and labor, with inconsistent results.
An industrial laser cleaner offers a contactless method of surface cleaning. Without abrasives, solvents, or excessive heat, it removes contaminants and coatings with micrometer-level precision. This aligns with the quality expectations in sectors where failure is not an option.
The Manufacturing Sectors Quietly Using It
1. Aerospace and Aviation
Aircraft components undergo routine maintenance and must meet regulatory standards for performance and safety. Any micro-contamination can impact fatigue strength, thermal properties, or aerodynamic performance.
Laser cleaning in aerospace is used to:
-
Prepare turbine blades for re-coating
-
Strip paint from fuselage sections
-
Clean welding zones on engine parts
Unlike chemical or mechanical cleaning, laser cleaning does not introduce microfractures or leave residues. Aerospace companies use industrial laser cleaners on titanium, aluminum, and carbon composites—all sensitive to traditional processes.
2. Automotive Industry
In high-volume automotive production, time is everything. Components like brake pads, gear assemblies, and powertrain parts require precise cleaning before coating or bonding. Laser systems are integrated into robotic arms for continuous, inline processing.
Common applications include:
-
Pre-welding oxide removal from steel panels
-
Cleaning injection molds
-
Removing oil residues from aluminum castings
OEMs and Tier-1 suppliers use industrial laser cleaners not just for quality control but also for traceability. Laser-cleaned surfaces exhibit measurable changes in reflectivity and morphology, making inspection and documentation easier.
3. Defense and Military Applications
Military hardware—from armored vehicles to aircraft carriers—faces corrosion from harsh environments. Cleaning and recoating these structures is part of lifecycle maintenance. Here, environmental and safety considerations are amplified.
Laser cleaning is used to:
-
Strip coatings from steel armor without degrading its ballistic properties
-
Clean weld seams on structural frames
-
Restore aged or corroded equipment in the field
Defense agencies favor laser cleaning because it reduces environmental waste and doesn’t rely on water, chemicals, or power-hungry compressors. Portability also plays a role, especially in field operations.
4. Electronics and Semiconductor Sector
As electronic devices shrink, component precision increases. Cleaning circuit boards, microchips, or microelectromechanical systems (MEMS) demands a method that won't scratch or deform tiny features.
Laser cleaning provides:
-
Selective removal of flux residues after soldering
-
Gentle cleaning of wafer surfaces
-
Pre-bond cleaning in micro-assembly
This level of finesse is not achievable with abrasive methods. An industrial laser cleaner becomes an enabler for miniaturization by ensuring microscopic cleanliness without touching the material.
The Science Behind Its Performance
A laser cleaner emits a high-energy beam that targets surface contaminants. The beam’s wavelength and pulse duration are tuned to match the absorption characteristics of the contaminant. This causes localized evaporation or ablation of the undesired layer, leaving the substrate intact.
For example:
-
Paint absorbs more infrared energy than aluminum, allowing the paint to be removed without affecting the metal.
-
Rust or oxides break apart at lower thermal thresholds compared to the steel beneath.
Laser cleaning systems offer precise control over energy density, beam diameter, scanning speed, and repetition rate. This control allows the system to adapt to different surface types—curved, flat, reflective, or textured.
Integration into Smart Manufacturing
In Industry 4.0 environments, automation and traceability are key. Industrial laser cleaners come with programmable parameters, vision systems, and PLC compatibility, allowing full integration into robotic cells or conveyor-based workflows.
Here’s how that plays out:
-
A robotic arm identifies and positions a workpiece using a vision system.
-
The laser head, mounted on a gantry or handheld frame, scans the surface according to a programmed path.
-
Sensors verify cleanliness via reflectivity feedback or thermal imaging.
This eliminates human error and enables repeatable results across thousands of cycles. In high-output settings, this level of automation isn’t a luxury—it’s a necessity.
Energy and Environmental Considerations
Traditional cleaning methods consume large amounts of water, chemicals, or media. Their waste requires disposal and regulatory compliance. Laser cleaning, on the other hand, is a dry, consumable-free process.
For example:
-
No solvents to store or dispose of
-
No secondary waste like sand or grit
-
Minimal PPE requirements
-
No venting or wastewater systems needed
This significantly reduces operational costs and regulatory complexity. Manufacturers under pressure to meet ESG targets see industrial laser cleaners as a compliance-friendly alternative that doesn’t sacrifice performance.
Long-Term Reliability and Maintenance
Industrial laser cleaners are built for longevity. With fiber laser sources offering lifespans exceeding 100,000 hours, and air-cooled models reducing moving parts, the need for maintenance is minimal. Systems can run continuously in harsh conditions—on the factory floor or in outdoor environments—without deterioration in beam quality or performance.
This translates to higher uptime, reduced service interventions, and predictable cost of ownership over 5–10 years of operation. For industries operating on lean principles or Six Sigma frameworks, that level of reliability is vital.
Common Misconceptions Dispelled
Myth 1: Laser cleaning is only for high-tech applications.
Fact: From railway tracks to food processing equipment, it is now applied across every sector with surface cleaning needs.
Myth 2: It damages the base material.
Fact: The laser’s energy parameters are carefully calibrated to remove only the surface contaminant without heating or affecting the substrate.
Myth 3: Laser systems are hard to operate.
Fact: Modern systems feature touchscreen interfaces, preloaded material settings, and remote support options, making them operator-friendly.
Cost Justification Without the Hype
When companies evaluate capital expenditures, return on investment (ROI) is a core factor. While an industrial laser cleaner might carry a higher upfront cost than sandblasting or chemical setups, the long-term savings are substantial.
Let’s consider just a few cost-cutting areas:
-
Elimination of consumables
-
Reduced labor (automated systems can be run by fewer operators)
-
Lowered downtime due to faster cleaning cycles
-
No waste disposal or air filtering equipment
Additionally, cleaner surfaces often reduce rework rates and extend the lifespan of coated or bonded parts—another form of indirect savings.
Final Thoughts
From aerospace hangars to automotive lines and precision electronics labs, the industrial laser cleaner has evolved into an essential tool for surface preparation and restoration. Its ability to operate without chemicals, media, or mechanical stress makes it not only practical but forward-looking—meeting the demands of performance, safety, and sustainability in one streamlined solution.
Organizations that recognize this are no longer asking if they should adopt laser cleaning. They’re asking how soon they can get it integrated into their critical workflows.