Dry Vacuum Pump Maintenance: Best Practices for Reliability and Longevity in U.S. Industrial Operations
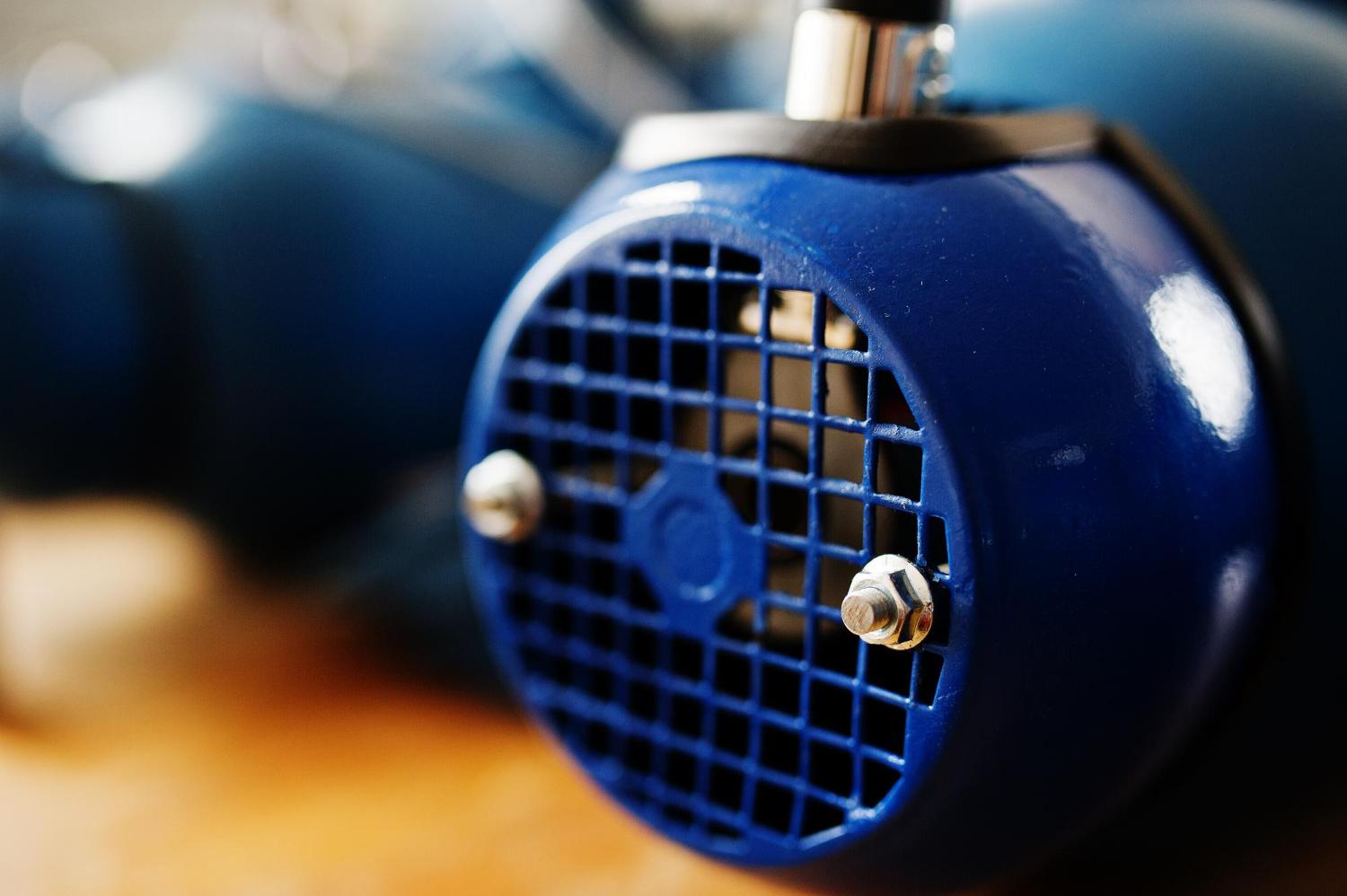
In a wide range of industrial, scientific, and manufacturing applications, vacuum technology plays a critical role in maintaining clean, controlled environments. Among the various types of vacuum systems, dry vacuum pumps are frequently chosen for their oil-free operation, reduced contamination risk, and overall efficiency. However, like all mechanical systems, these pumps require consistent upkeep to ensure optimal performance. Dry vacuum pump maintenance is therefore a critical element in protecting process integrity, minimizing downtime, and extending equipment lifespan.
As dry vacuum pumps are used in semiconductor manufacturing, pharmaceutical production, chemical processing, food packaging, and research laboratories across the United States, maintenance practices must be aligned with environmental standards, operational demands, and system complexity. This article explores the core principles, strategies, and challenges associated with maintaining dry vacuum pumps in industrial settings.
Understanding Dry Vacuum Pumps
Dry vacuum pumps differ from traditional oil-sealed pumps in that they operate without lubricants in the pumping chamber. This design reduces the risk of contamination, making them ideal for cleanroom environments and sensitive applications where oil vapor or particle emissions could be detrimental.
Several types of dry vacuum pumps are commonly used, including:
-
Scroll Pumps
-
Roots Pumps
-
Screw Pumps
-
Claw Pumps
-
Diaphragm Pumps
Each type has specific maintenance requirements, but all rely on clean mechanical operation, precise tolerances, and protection from particulates or corrosive gases to maintain performance.
Why Dry Vacuum Pump Maintenance Matters
Dry vacuum pumps are engineered for reliability, but their performance can degrade without proper care. Maintenance helps prevent mechanical failures, ensures energy efficiency, and protects downstream systems. In U.S. industries where regulatory compliance and productivity are paramount, unplanned downtime due to pump failure can result in significant financial losses and operational delays.
Key reasons to implement a proactive dry vacuum pump maintenance program include:
-
Preventing premature wear of components
-
Maintaining vacuum integrity and process stability
-
Reducing contamination risks
-
Optimizing energy consumption
-
Ensuring compliance with safety and emissions regulations
Routine Maintenance Activities
A successful maintenance routine for dry vacuum pumps involves both scheduled inspections and responsive servicing. The frequency and extent of these activities may vary depending on application intensity, ambient conditions, and the specific pump type.
1. Visual Inspection
Regular visual checks can reveal early signs of wear or malfunction. This includes:
-
Checking for vibration or unusual noise during operation
-
Inspecting the motor housing and seals for leaks
-
Monitoring exhaust outlets for excessive particulate matter
-
Ensuring that filters and inlet screens are clean and intact
Such inspections can often be conducted daily or weekly as part of a broader preventive maintenance program.
2. Temperature and Vibration Monitoring
Monitoring operational temperature and vibration levels helps detect imbalances, misalignments, or thermal issues. An increase in either may indicate internal component stress or pending mechanical failure. Using sensors or predictive maintenance tools can assist with early diagnostics.
3. Cleaning and Debris Removal
Over time, particulates and process byproducts can accumulate within the pump or at its inlet. Scheduled disassembly and cleaning of internal surfaces (where permissible) help maintain vacuum performance and reduce wear on rotors and casings.
In industries such as chemical manufacturing, residue buildup may require the use of neutralizing agents or controlled cleaning procedures to prevent corrosion or blockage.
4. Filter Replacement
Inlet and exhaust filters are critical to protecting the pump from contaminants. Regular replacement or cleaning of filters is one of the most effective ways to extend pump life. Neglecting this aspect of maintenance can lead to clogging, back pressure, and eventual failure.
Filter replacement schedules typically range from monthly to quarterly, depending on the operating environment.
5. Seal and Gasket Inspections
Seals and gaskets are wear components that help maintain internal vacuum and prevent external air leakage. Over time, these parts may harden, crack, or degrade, especially under extreme temperature conditions. Routine inspection and replacement are essential to preserving vacuum performance.
Scheduled Servicing and Overhauls
In addition to routine maintenance, most manufacturers recommend scheduled servicing at fixed operating hour intervals—commonly at 10,000-hour and 20,000-hour marks, though this may vary.
Servicing during these intervals often includes:
-
Complete disassembly of internal components
-
Inspection of rotors, shafts, and bearings
-
Replacement of worn parts
-
Rebalancing and reassembly
-
Performance testing and validation
Regular overhauls help restore pumps to near-original performance and reduce the likelihood of catastrophic failure.
Maintenance Challenges in Industrial Environments
Although the principles of dry vacuum pump maintenance are well-established, several challenges arise in real-world operations across U.S. industries:
1. Contaminant Exposure
In many sectors, pumps are exposed to corrosive gases, solvents, dust, or reactive chemicals. Over time, these materials can damage internal surfaces or interfere with mechanical tolerances. Selecting appropriate pump materials and using protective gas purges can mitigate this risk, but maintenance must remain vigilant.
2. Lack of Trained Personnel
Maintenance requires both technical expertise and familiarity with pump operation. In some facilities, a lack of specialized training can result in skipped procedures or improper servicing. Investing in technician education and manufacturer-aligned maintenance protocols is key to long-term success.
3. Operation Beyond Design Parameters
Running pumps at higher speeds, pressures, or duty cycles than intended can accelerate wear. Maintenance teams must understand the design limitations of each unit and monitor system parameters closely to ensure operation within safe boundaries.
4. Supply Chain Delays for Parts
Access to replacement parts or tools may delay necessary maintenance. Keeping a stock of critical spares on-site and maintaining a well-organized maintenance schedule can reduce downtime due to procurement issues.
Best Practices for Effective Dry Vacuum Pump Maintenance
Implementing a structured maintenance program ensures consistency, reliability, and safety. Best practices include:
-
Developing a Maintenance Log: Record all inspections, part replacements, and performance data. This historical information can help identify trends and predict future needs.
-
Following Manufacturer Guidelines: Adhering to OEM-recommended intervals and procedures ensures compatibility and performance integrity.
-
Scheduling Preventive Maintenance: Establish regular service intervals based on usage and operating conditions, rather than waiting for performance degradation.
-
Training Staff Regularly: Ongoing education ensures that maintenance personnel understand evolving technologies, safety requirements, and correct procedures.
-
Using Condition Monitoring Tools: Sensors, thermal imaging, and vibration analysis can detect early faults and reduce unplanned downtime.
Compliance and Environmental Considerations in the U.S.
Dry vacuum pumps offer advantages over oil-sealed systems in terms of emissions, waste handling, and cleanliness. However, U.S. facilities must ensure that all maintenance practices comply with applicable regulations, such as those set by:
-
The Environmental Protection Agency (EPA) for air quality and emissions
-
Occupational Safety and Health Administration (OSHA) for workplace safety
-
Local and state environmental boards regarding chemical handling and waste disposal
Proper maintenance helps maintain compliance by preventing leaks, minimizing hazardous waste, and reducing energy consumption.
Conclusion
As vacuum technology continues to play a critical role across diverse sectors in the United States, the importance of consistent and comprehensive dry vacuum pump maintenance cannot be overstated. Whether in a pharmaceutical laboratory, a semiconductor cleanroom, or an industrial manufacturing plant, maintaining these systems is essential for operational efficiency, equipment longevity, and process integrity.
By adopting structured maintenance routines, using real-time monitoring tools, training staff, and staying aligned with regulatory standards, facilities can ensure that their dry vacuum pumps operate reliably and safely for years to come. As technology advances, so too must the strategies used to maintain it—ensuring that innovation and reliability move forward together.